The Oookies!
By George Lanthier*
This is from our book, Advanced Residential Oilburners, Figure 1, and addresses a problem that it seems the oil service business will have to learn to live with, like it or not, the oookies. Will they ever end? This article is about the oookies, a subject that has grown near and dear to those you make their living turning the screwdriver and keeping the home fires of oilheat burning, yep, my people, the service technicians. It is the week before Christmas, 2015 and we may be headed towards another winter that wasn’t. It seems that after two tough winters we have already forgotten what a warm winter can do to equipment.
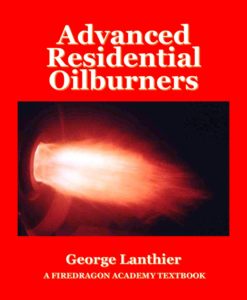
First, I am going to go out on a limb, (so where else would you expect to find me), and blow up a few bridges (yeah, so what else is new). The subject is a phenomenon now called the “cold-soaks” or “running saturations,” and for some others simply “the oookies.” Now for those of you who are weak-at-heart–bail out now. This is where the excrement meets the blower wheel.
There are two smells that technicians have come to know and dread. The first is when a customer has cherryed or dry fired a cast iron boiler. It is like no other smell in the world, right? Even when you go to a cast-iron foundry you expect to smell that smell but nope, it’s different.
The other smell is from a particular type of plugged boiler. Not an average plugged boiler, but a particular type of plugging. Let me give you a description of this wonderful scene and cause some of you a daymare, Figure 2.
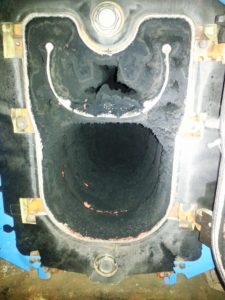
First, the boiler is plugged from the bottom of the unit to maybe the top of the chimney. The soot in the base of the unit is soft and fluffy and as you work your way up the soot gets harder and crustier.
The soot in the chamber area may be what appears to be oil-soaked and one of the dumbest things ever said by any of us is, “thank God it didn’t light off.” Now, why is this statement dumb? Because it was running when it went off. Yep, when the cad-cell finally shut it off it was still running.
Ever try to light some of this oil-soaked (?) soot? You need a torch! That’s because fueloil is 85% carbon and 15% hydrogen, remember your basic oilheat theory? And so, my friends, the hydrogen has been burned off and now you are stuck with something that is basically liquid carbon and why they call it cold-soaked. The hydrogen and ignition factor is gone, done an Elvis and left the building, checked out of the Hotel California, finite and poof!
Some other things we do know about a typical cold-soaked unit are:
- They happen predominately on wet-base boilers, steel or cast-iron.
- They happen mostly to non-chambered units.
- They happen on cold-start boilers providing domestic hot water. Not a good idea anymore and probably never was. We have discussed this before in previous articles.
- They happen mostly on burners with intermittent (constant) ignition that have three wire primary controls. Burners with interrupted ignition are not immune, but it does seem to help, a lot.
- This situation did start occurring before red-dyed fuel and biofuels. So, those theories don’t hold, but I am not ruling out that they may not have an effect, and I still question what these modern fuels are doing to the servicing of oilburners.
- No brand of burner is exempt.
- No brand of boiler is exempt.
- Nobody really, really knows why this is happening, really?
So, what do we do?
Well, let’s look at some more facts.
- Cad-cells should only see direct light and the tubes of burners should never be painted silver, white or any other color than black or other dark paints. The stupid practice of painting tubes allows stray, indirect light to travel back to the “eye” and cause and allow the unit to go to a higher degree of pluggedness. People who do this are extremely dangerous.
- Fact! You must maintain Ignition Point for fueloil to burn cleanly, hot and safely. The ignition point of fueloil is now below 500° F. Below that you are making smoke, period. This fact is not open for debate– it’s physics, I don’t know physics but I know oilburners.
- When you open your inspection or swing-door or remove the burner mounting plate, you will find a perfect hole within the soot in the combustion area. That hole in the soot is caused by the high static fan and air handling parts that make up your high velocity retention head oilburner, that’s good! At least that was trying to keep the burner running right up to the very last second.
- Draft (airflow) is the most important factor in the combustion process. The problem is that as boilers are becoming tighter, to become more efficient, draft is reduced through pressure drop and temperature. Always remember this golden rule about draft. Cut or lower the stack temperature by 50%, and you lower the thermal draft output by 50%.
Okay, so many of us claim we really don’t know what’s happening out there, but let’s look at what some of my friends has done since running across cold-soaks in the late 1980s. By the way, they do this after each cold-soak and have never had a repeat call or rework as many are calling these things now.
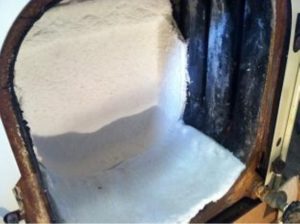
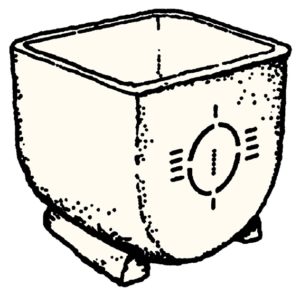
- Install a partial, Figure 3, or even better a full chamber sized to the firing rate used. This can be done very easily using something like the Lynn Quickee or bathtub type design, Figure 4. This will ensure that ignition point is maintained and the fire stays hot. We’ve found over the last 30 years that any chamber is better than none at all. True, the water content of a boiler makes a huge difference and bigger is not even close to being better.
- Fire the boiler to within 25% of the maximum firing rate. This does two things. First, it creates and help keeps a larger temperature differential between the thermal draft elements. This allows the burner to make as much thermal draft as possible. This is very important for summer operation.
Second, it allows the boiler to fire within the outlines called out by the manufacturer, the ASME and the DOE for optimum and correct performance and operation. - Go to interrupted ignition operation. The interrupted ignition prevents the burner from running with a borderline fire that can happen with intermittent ignition and in my opinion that is not only a better operating burner, it’s a safer one.
- Add a pre-purge cycle. Pre-purge is what sets off a good installation from a great one!
A pre-purge cycle is always used on commercial and forced-draft installations–think about that and ask yourself why. The purge doesn’t have to be long, and even a few seconds is better than nothing. Did you know that with the burner design that came before the retention head, the Shell-head, no burner was ever installed without a delayed oil valve? Also, have you ever seen a commercial burner or industrial burner without one? Okay, you knew, but do you know why? - Always set up the burner for a “Trace of Zero” on the Lanthier Scale, Figure 5. This provides for a minimum of excess air while preventing operation at any smoke level. “Trace of smoke” is dead. Today’s oilburners don’t have to make smoke, so why are you?
- Increase your summer hot water control differential from 10°F to 20°F or more. The longer the run cycle the better chance you have of getting everything hot and it sure helps to make better thermal draft too! With today’s controls, Figure 6, up to 45°F differentials can make a big difference in summer and winter burner operation.
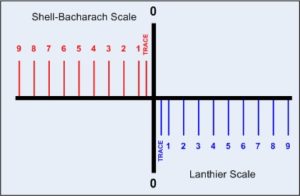
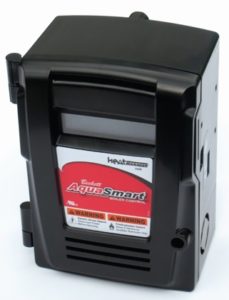
Well, that’s my story and slant on the oookies. Maybe not the one answer, but a few more things to look at and check. As we get more on this we will let you know, and yes Virginia, oil quality and cleanliness and the need to move to low sulfur oil all has an effect on this problem. However, I just have to ask, when are we going to do something about those problems and stop talking and whining about them?
By the way, the reason commercial and forced-draft burners always use a pre-purged oil valve is simple. It allows the burner to establish draft flow, volume and direction. In English, it just works better. As for the other question on Shell-heads, here’s the official word from the Shell Oil Co., who developed it; “…the purpose therefore is to allow the fan to come up to operating speed and to give direction to the draft before oil is introduced for burning.” Interesting, huh?
Want something even more interesting? Did you notice that the issue of higher pump pressures in regards to cold-soaks didn’t come up, even though many think that higher pump pressures will fix all that is wrong with the world? That’s just the point, in my opinion pump pressure is irrelevant, no issue, a zippo factor when it comes to the oookies.
Finally, and in case you’re interested as to what the oookies do to a chimney check out Figure 7 and Figure 8 sent to me by my friends at the Chimney Sweep Institute of America, the chimney pros. So, what do I really feel is the solution to the oookies? Read this read article again. You’re not getting it, and that’s just the point!
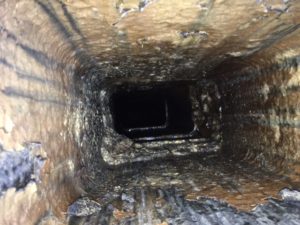
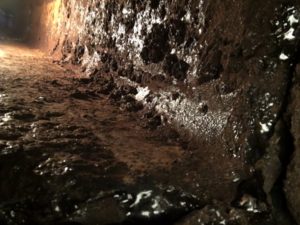
See ya.
*George Lanthier is the owner of Firedragon Academy, a Massachusetts Certified School teaching heating subjects around both gas and oil. Firedragon Academy has its hands-on training facility in Sturbridge, Massachusetts at the Beckett Training Center. Firedragon is also a publishing firm publishing George’s over 60 books and manuals on HVAC subjects. He is a CETP, NATE, NORA, PMAA and PMEF Proctor and has been a Massachusetts Certified Instructor since 1975. He can be reached at 608 Moose Hill Road, Leicester, MA 01524. His phone is 508-421-3490 and his website can be found at FiredragonEnt.com